MQLによる工場の環境改善が、多くの加工現場で進められる。ヤシマ金属(株)は,工場の環境改善に成功しただけではなく、同時に工具コストの大幅削減を達成するなど、多くのメリットを引き出している。 |
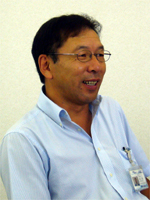 |
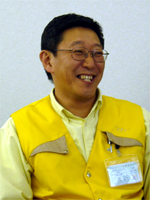 |
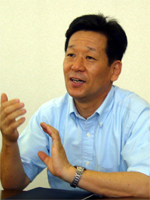 |
代表取締役社長
橋詰春彦氏 |
取締役工場長
馬場宏幸氏 |
(有)蓼北技研工業
営業技術
糊沢住典氏 |
|
ヤシマ金属(株)(長野県佐久市矢島700,TEL.(0267)58−2800)は、エンジンピストンメーカーであるアート金属工業(株)のグループ企業として,アルミエンジンピストンの鋳造を手がける鋳造メーカーである。鋳造したピストンから湯口という不要部分を切り離す切断加工にMQLを適用,大きな成果をあげている。
導入のきっかけは,工場の建て替えに伴って仕事の見直しを図ったこと。同社で鋳造されるアルミのエンジンピストンは月産50万個。最大9種類のアルミを手がけてきたが,現在はある程度統合して5種のアルミを手がけている。ピストンの種類は月に200機種ほど,全体では800機種に及ぶ。最小のロット数は1個から。平均ロット数は約2、000個。それまでは種類が変わるたびに必要な段取り替えに多くの時間を費やしていた。小ロットの製品の場合,段取り替えに時間をとられ,思うように利益を確保することが難しかった。そこで段取り時間を「それまでの90分から10分に」(代表取締役社長・橋詰春彦氏)という目標のト下,大幅な作業の見直しが行なわれた。その過程で,「湯口の切断工程]も見直された。それまで,親会社で使用されているものと同じであった切断機を見直し,自社の事情にあった独自の設計による切断機の開発が行なわれた。
鋳鉄とは異なりアルミ鋳造では,鋳造品が収縮して容積が大きく変化する。それを補うために通称「押し湯」と呼ばれる補助的な部位を大きくつける必要がある。製品の両側についた大きな耳のような部分である。これは後工程にはまったく不要なため,鋳造後切り落とす必要がある。それを行なうのが湯口切断機である。
アルミ材の切断は,水溶性切削油をかけながら超硬チップソーを高速に回転させて行なわれることが多い。従来同社でもそのような方式で行なわれていた、超硬チップソー(コールドソー)を使用し,加工条件は切削速度960m/min,1刃当たり0.01mm,送り720mm/minというもの。高速切断では良好な加工面と加工精度が得られるが,反面,水溶性切削油がミストとなって工場に拡がり,床が油で濡れる,また高温の環境下で水溶性切削油が腐敗して臭いが発生するなどの問題があった。また,高速に回転する工具による騒音も激しかった。 さらに出てくる切屑が薄いため,再溶解するときに中の空気が断熱材となって歩留まりが悪いという欠点もあった。
もともと鋳物工場は「熱」による環境が厳しい職場。そこで「熱と騒音のどちらか一つでも,なくしたかった](橋詰氏)とのこと。また鍛造品では,水分が内部欠陥につながり,また水分の混入で水蒸気爆発の危険もあるため,水分をなくすことも目標の一つとされた。
|
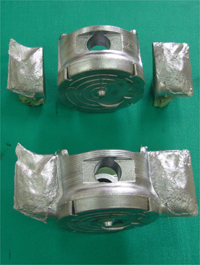 |
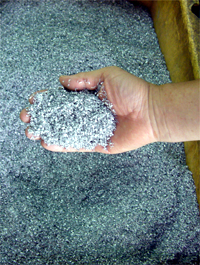 |
アルミ製ピストンとその湯口。
本体に比べて湯□もかなりの
ボリュームがある。 |
切断時に出る切屑。ドライな状態。 |
|
低周速切断(低回転、高送り)で大幅に改善 |
まず,従来の高速回転ではなく,工具を低速で回転し、大きな送りで切断する「低周速切断方式」が試みられ,試行錯誤の上,水溶性切削液を使用する新しい切断機の機構が完成した。これは,工具(丸鋸)を低速で回転させながら,高送りで大きく切り込んで加工するというもの。加工対象がアルミの一般材であるAC8A材の場合,ハイスのメタルソーを使用し,加工条件は、切削速度94m/min,1刃ありたりの送り0.1mm、送り900mm/minである。機械本体は、多品種小ロットに対応できるよう、ワークサイズに簡単に対応できるようにしたほか,機械全体の剛性,またクランプの剛性を高めるなどの工夫が施された。また,加工効率が高いため,それまでの切断機に比べ容量の小さいモータが採用された。
機械の開発を担当していた楜沢佳典氏(現・蓼北技研工業)は、その時点でセミドライ法を知り,ブルーベセミドライシステム(フジBC技研(株)製)を導入する。それまでは一般的に加工に伴う熱を排除するためにも水溶性切削液が大量にかけられていたため,当初は「その効果を信じられなった」(楜沢氏)という。しかし,これが別の大きな効果も発揮する。
まず,油の使用量が激減したため、それまではべたついていた床が乾いた状態となり,工場の環境が大きく改善した。大量の切り取られた湯口や切屑は,再溶解してアルミの素材として使用されるが、従来は再溶解前に付着している水分を取り去るため大きなロータリキルンの中で油分を燃焼させていた。しかしセミドライシステムの採用で, 乾燥させる工程自体が不要となった。さらに,当初は予想できなかった大きな効果の一つが工具寿命の大幅な向上である。
|
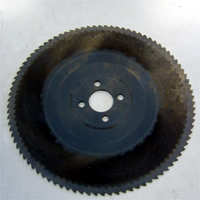 |
新品のメタルソーに、再研削を行なったメタルソーを重ねたところ。
約20回、直径φ300mmがφ260mmまで再研削して使用される。 |
|
エ具寿命の大幅向上 |
ダイヤモンドチップソーに水溶性切削油の組み合わせで行なわれていたそれまでの工具寿命は工具1枚当たり3万個程度、それが新方式でハイスのメタルソーによる低速回転,高切り込み,さらにセミドライシステムの適用で、1枚の工具で10万個以上の加工が行なえるようになった。さらにこの1枚約1万5,000円のハイスメタルソーは,直径が当初の直径φ300mmからφ260mmになるまで20回ほども再研磨され使用される。
ただ,これらの条件がどの場面でも「保障されるものではない」(楜沢氏)という。少なくともここで使用しているAC8A材もしくは近似の合金には非常に有効なことは間違いない。アルミは含まれる金属で性質が大きく変わるため,すべてに同様な効果が保障されるものではない。ハイシリコンアルミの場合、同社ではハイスのメタルソーではなく,超硬のチップソーを使用している。しかし,その場合にも低周速,高送り,セミドライシステムの組み合わせで高い効果をあげている。グループ内で,ハイシリコンアルミを手がけている事業所の例では,従来方式では,1枚の工具で数百個の加工しかできなかったものが,この方式とすることで数万個加工できるようになった実績も報告されている。
ただし,セミドライシステムが万能ではない。ここで使用されているセミドライシステムの場合,供給される植物性油が高い潤滑性能を発揮するものの,冷却効果は期待できない。また,一般の切削油供給で行なわれる切屑の洗い流しは期待できないため,切屑が自然落下する機械構造が必要とされる。
|
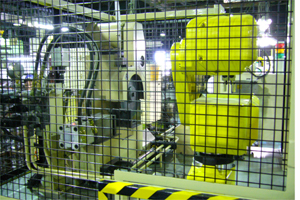 |
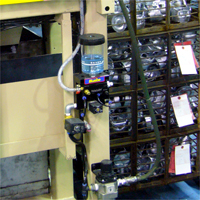 |
ロボットによって、計測工程も自動化した切断機。 |
切断機に取り付けられたセミドライシステムの油給油装置。水溶性切削油を激減させた。 |
|
なぜ、エ具寿命がのびるのか |
「低周速切断方式]を確立した楜沢氏等は,以下のように推論する。新しい工具を使用開始してから切断ロット1,000個を超える辺りから切断が安定する。同時にアルミの刃先への溶着が始まる。つまり溶着したアルミが構成刃先となり,本来の刃先を保護して切削が進むと考えられるということだ。
刃先に溶着が起きているから,面租度は悪くなる。しかし,この「湯口切断」では,後工程でmm単位の取りしろがあるため,ここでの面租度は要求されていない。
このように,剛性の高い切断機をベースにして,低価格なハイスメタルソー,さらに工具の低周速高切り込み方式,セミドライシステムの組み合わせは、当初の予想をはるかに超えた効果をもたらしている。
工場環境の改善,大幅なl工具寿命の延長などの実績により,「親会社であるアート金属工業のグループ企業全体が,ここで開発された切断システムを採用し,効果をあげている」(工場長・馬場宏幸氏)。さらに外部の同業者からも発注を受け,自動車部品メーカーには,さまざまな材質のピストン鋳造品の湯口切断専用機を,またダイカストメーカーにはスクイズ成形品のゲート部およびオーバフロー部同時切断の専用機などの供給を行なっている。
ヤシマ金属(株)は,自社の現場ニーズに合った技術の追求,設備開発,選択によって有効な技術を確立した。この技術がすべての加工現場に応用できるものではないものの,今後は,必要としている外部の現場へも広く貢献していく。
(本誌 小山 宏)
|
|
改善結果と効果 |
■生産性向上 切断機による改善 |
少量多品種対応
【前】段取替えに時間がかかった
【後】段取替えが短時間になった |
生産性
【前】機械15台 8人で月産30万個
【後】機械10台 5人で月産50万個 |
再溶解
【前】切り粉が薄く空気層が多いため、 溶解に時間がかかった
【後】切り粉の比重が重くなり、溶解しやすくなった |
切断機コスト
【前】300万円/台
【後】600万円/台 |
■生産性向上 セミドライシステムによる改善 |
再溶解
【前】ローターリーキルンによる乾燥が必要
【後】切り粉が乾いているので、乾燥工程なしで 再溶解できる |
濃度管理
【前】水溶性の濃度管理に手間と時間がかかった。 また、濃度をうまく管理し切れなかった。
【後】オイルポットの油量を確認するだけ |
■生産性向上 切断機改善とセミドライ加工採用の相乗効果 |
工具寿命
【前】水溶性の濃度によりバラつく。 丸ノコ1枚あたり30,000個カット。
【後】ブルーベ植物油によって飛躍的に向上した。 丸ノコ1枚あたり100,000個カット。 |
環境面の改善効果 セミドライシステムによる改善 |
汚れと掃除
【前】切りくずが薄いために、飛散しやすかった。機械回りや床が水溶性切削油で常に汚れていた。また、切り粉が濡れているため、掃除がしにくかった。
【後】切り粉が重いために、飛散しにくくなった。
切り粉が乾いているので、機械や床が簡単に掃除できるようになった。 |
腐敗
【前】腐敗臭がひどかった
【後】腐敗臭がなくなった |
消費油量
【前】原液150L/月(希釈後4500L/月)
【後】20〜30L/月 |
環境面の改善効果 切断機よる改善 |
騒音
【前】高音域の騒音が問題化
【後】騒音が抑えられた |
|
|
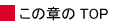 |
Copyright esPLANET2004 |