地球環境保全は21世紀の最優先課題として認識されており,機械加工分野においても幅広い領域で対策が検討,実施されている。その中でも省エネ,廃棄物低減に大きく貢献できるドライ,セミドライ加工(以下これらを広義のドライ加工として記述する)技術は研究が盛んに行なわれており,フライス加工,歯切り加工などで実用化されている。しかしながらアルミ材,特に穴加工では溶着による刃具折損,精度悪化など課題が多く,実用化事例はまだまだ少ない。
われわれは数年前からアルミ材のセミドライ加工技術の開発を進めており,6製品7ラインの部品加工で実用化している。本稿では,その開発・実用化事例を紹介する。 |
1 環境対応技術の動向 |
機械加工分野における環境対応技術にはさまざまなものがあるが,大きく省エネ,廃棄物低減,作業環境の安全・快適性確保に分類される(図1)。
省エネに関しては,配管抵抗低減による切削油ポンプのダウンサイジング,油圧レス化1)などがあげられる。常時運転しているポンプ類は,定格電力が小さくても消費電力は大きくなることが多い。特に切削油に関する消費電力は全体の60%を超える例もあり(図2),対策が望まれている。
廃棄物低減の対象は主に切削油であり,各社で切削油のロングライフ化,リサイクル化などの取り組みが行なわれている。2) ロングライフ化では,切削油のシンセティック化が一つのアイテムとしてあげられる。シンセティック切削油は化学的に合成した油剤を基油として用いるため,水との親和性,分子量などを自由に設計でき,カルシウムなどの金属イオンや他油の混入による界面活性剤の劣化,油水分離を抑制することが可能である。ただし,設備への攻撃性(スライド潤滑油の洗浄現象,洩れによる電気系統への影響など)や廃水処理性には十分に注意する必要がある。
作業環境の安全・快適性確保の最近の取り組みとしては,切削油の塩素フリー化があげられる3)。塩素系化合物は極圧添加剤として高負荷用の切削油中に含まれており,高温切削時,また廃油の燃焼処理時に猛毒であるダイオキシンを発生させる恐れがある。塩素系切削油がJISから除外されたこともあって,各油剤メーカーでは塩素フリー化の開発が進んでおり,従来品と同等の性能を持つ新油剤が揃いつつある。
このように,環境対応技術には切削油というキーワードが多く含まれている。切削油を大幅に低減できるドライ加工技術は,すべての環境対応技術に共通する開発課題であり,多くの企業,研究機関が活発に開発を行なう大きな理由となっている。以下では当社の開発概要を述べる。 |
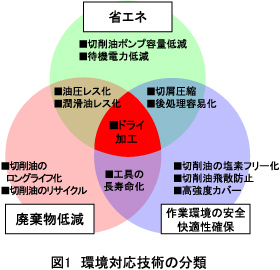
|
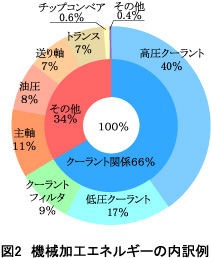
|
2 ドライ加工技術開発の考え方
|
開発を行なうに当たり,対象とする工法,材質を検討した。当社ではアルミ材の製品が多いこと,またアルミ材穴加工に関する刃具メーカーや研究機関の開発事例はきわめて少なく開発の必要性が高いことなどを考慮し,アルミ材のドリル,タップ,リーマ,ボーリング加工法を開発ターゲットとした。
ドライエ法では,切削油の役割である潤滑,冷却,切屑排出性能をバランス良く持ったセミドライ加工を選択し,ミスト供給方式はセンタスルー外部ミキシング方式を開発のベースとした。(図3) 外部ミキシング方式は,ホーコス(株)などが提唱する内部ミキシング方式に比べて供給できるミスト量は少ない傾向があるが,技術の核となるミスト生成部に対する開発の自由度が高い。またスピンドルの内部構造を大きく変更する必要がないため,さまざまなメーカーの設備への展開が容易である。
加工能率(送り速度F),精度に関しては,開発期間を考慮した上で湿式と同等以上の領域を狙うことが必要であると考え,国内外のベンチマークを基に目標値を設定した(図4)。
|
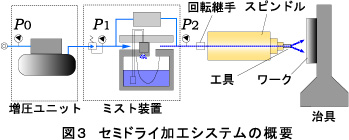
|
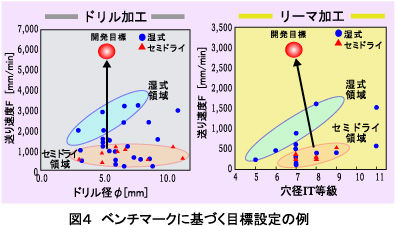
|
3.開発技術
3.1 ミストの生成・供給技術 |
すべての工法を通じて,ミストの生成・供給技術は重要である。求められる要素はさまざまなものがあるが(表1),以下では安定的なミスト生成に関する技術を紹介する。
一般的に,ミストはベンチュリと呼ばれる部分において,エアの力で油を吹きちぎる方法で生成される。ミスト生成能力は,主にベンチュリ前後のエアの圧力差(以下差圧)に依存するが,小径刃具ではオイルホール(以下O/H)径が小さいため十分な差圧を確保できず、ミスト量が大きく低下する。それを防ぐため,ミストの一部(エア分のみ)を大気へ開放して差圧を確保する場合があるが,エアが無駄になってしまう問題点がある。また,離散的な制御になるため工具ごとの適正制御ができず,0/H断面積によって差圧が変化し,ミスト量がばらついてしまう。
そこで,油剤を横から吹きちぎる構造により,小さな差圧でも大きなミスト生成能力を持つ特殊ベンチュリと,異なるO/H断面積でも差圧を一定に制御できる技術を開発した(図5)。これにより,工具サイズにほとんど依存しない,高く安定したミスト供給を実現することができた(図6)。
そのほか,エルボ配管の廃止,エアの増圧とバッファリングなどにより,ミストの圧損,凝結の最小化,切屑排出性向上を実現している。
|
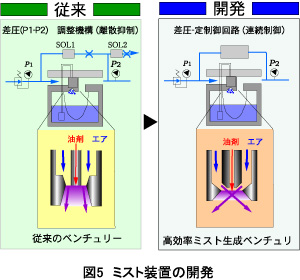
|
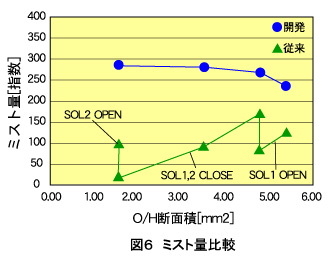
|
3.2 ドリル加工技術 |
ドリル加工は単位時間当たりの切屑除去体積が大きく,また閉鎖的で熱が放出されにくいため,難易度が高い工法の一つである。以下はM6下穴を想定した開発事例で,目標値は送り速度F=6,000mm/minと設定した。
開発当初の基礎実験では,切屑の溶着により刃溝に切屑が詰まり,折損が発生した(図7)。N数を増やして実験したところ,加工可否は刃先の温度が関係していることが分かった(図8)。これらより,ドリル折損のプロセスを図9のように推測し,「刃先温度」を評価項目の一つとして開発を行なった。
通常ミストは刃具の先端部から吐出するが,実切削時間は非常に短く,その間しかミストが有効に働いていない。また刃溝へのミスト供給は溶着を抑制する上で重要であるが,切屑が邪魔をするという問題点がある。そこで,工具外周部からもミストを吐出する構造とした(図10)。われわれはこの手法を「グルーブ(溝)スルー」と呼んでおり,コレットの内周部への溝形成,刃具シャンク部への溝・穴の形成など,工法によって形態はさまざまである。これにより,アプローチ,軸移動などの非切削時間を利用して刃溝にミストを付着させることができ,さらにミストエアによる冷却効果が得られる(図11)。ただし,適正な設計を行なわないと十分な効果が得られず,逆に切屑排出性を妨げる場合もあるので注意が必要である。
また,適正な刃具形状を決定するため,刃具形状要素の違いによる刃先温度への影響を調査した(図12)。その結果,シンニング,心厚,0/H径の影響が大きいことが分かった。中でもシンニングの影響はもっとも大きく,チゼル部の切れ味は劣るが切屑の流れを円滑にできるスリーレーキが優れており(図13),切屑の流れに関して十分な注意を払うことが重要であることが分かった。
刃具へのコーティングは,耐溶着性を考える上で重要な要素である。コーティングにはさまざまなものがあるが,効果が見られたのは,DLC(Diamond
Like Carbon)コートと超微結晶ダイヤモンドコート(結晶粒径が1μm程度と小さく,通常のダイヤモンドコートより表面が平滑な特徴を持つ。(図14参照)であった。特に超微結晶ダイヤモンドコートの効果は高く,F=10,000mm/minでも溶着はほとんど発生しなかった(図15)。
しかしDLCコートを含め,密着性,コストなどの課題が残されており,実用には十分な注意が必要である。以上の盛り込み(コーティングを除く)により,目標値である送り速度F=6,000mm/minを達成できた。量産加工での刃具摩耗評価結果を図16に示す(この例では,ワーク剛性が低いこと,工具長が長いことから,送り速度を落としてある)。セミドライ加工のほうが摩耗量は小さく,良好な切削を実現できていることが分かる。
|
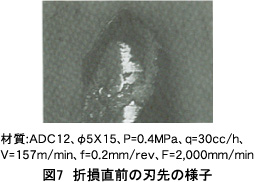
|
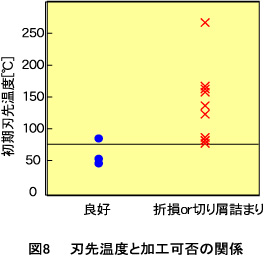
|
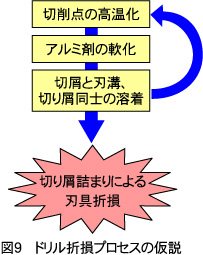
|
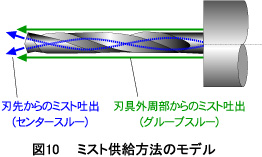
|
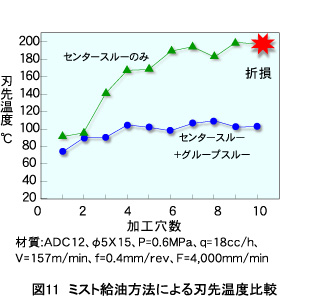
|
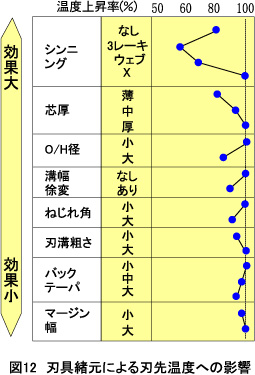
|
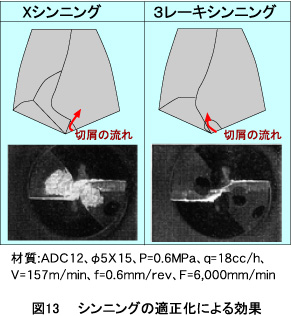
|
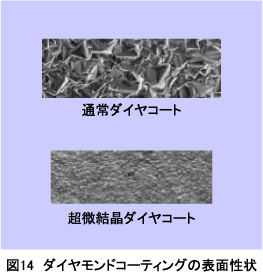
|
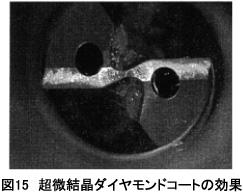
|
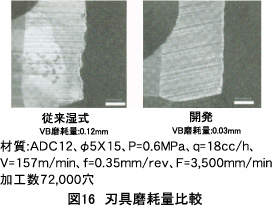
|
3.3 タップ加工 |
めねじ加工には切削,転造,ねじフライスといった工法があるが,以下では切削タップ加工に関する開発事例を述べる。目標値はねじ精度JIS
2級を満足し,ねじ山形状が湿式と同等以上,送り速度F=3,000mm/minと設定した。
切削タップ加工における技術課題は,切れ味低下によるむしれの抑制である(図17)。むしれが発生する直前のねじ山を拡大してみると,追い側のこば欠け量が湿式に比べ大きいことが分かった。
高速加工用のスパイラルタップでは追い側切れ刃の実質的なすくい角は負となり,切れ味が低下する。湿式では問題にならないが,セミドライではこの影響が大きいと考えた。
そこで,ねじれ角,すくい角によるこば欠け量の変化を実験により評価した。その結果,ねじれ角小,すくい角大とすることで,追い側こば欠け量を大きく低減できることが分かった(図18)。
また,前節で紹介したグルーブスルーを含め,ミスト供給方法を適正化することで止まり穴,通し穴両方でねじ形状をバランス良く向上できることが分かった(図19)。量産加工での刃具摩耗評価結果を図20に示す。摩耗量は湿式よりも小さく,ねじ山形状も良好であることが分かる。
|
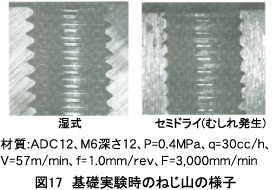
|
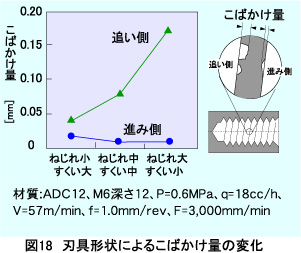
|
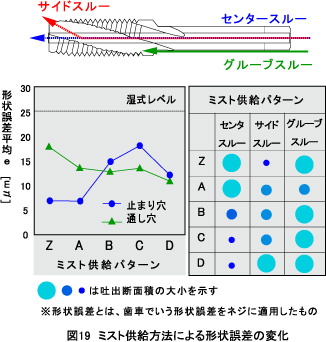
|
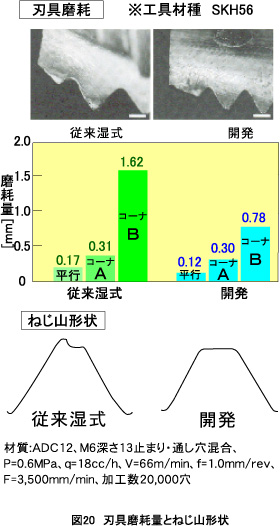
|
3.4 リーマ加工技術 |
以下に紹介するのは,鋳抜き穴からの一発加工を想定した比較的取りしろの大きい(φ2程度)リーマ加工に関する開発事例である。目標値は面粗さ3.2Z,真円度0.005,送り速度F=3,000mm/minと設定した。
リーマ加工の技術課題は,刃先,ガイドパッドヘの溶着抑制である。超硬バニシングリーマを用いた基礎実験後の刃先の様子を図21に示す。リ−マ加工は高い加工精度が要求されるため,このような大量の溶着はもとより,わずかな溶着でも品質に大きな影響を与える。
切れ刃の溶着を抑制するため,ねじれ角,コーティング,切れ刃材質などに対して実験を行なった結果,切れ刃の焼結ダイヤ化がもっとも効果があることが分かった。
また,従来はガイドパッドが加工面と接触することで真円度、面粗さを確保する構造であったが,超硬部と加工面との接触による溶着を抑制するため,切れ刃マージン部のみが加工面と接触する段付き多刃構造とした。こうすることで加工面を形成する切れ刃の負荷を低減すると同時にガイド性を確保でき,精度向上を実現できることが分かった(図22)。
これらを盛り込んだ刃具での実験結果を図23に示す。目標の品質,加工能率を十分満足していることが分かる。
|
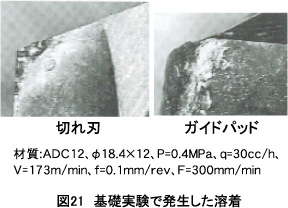
|
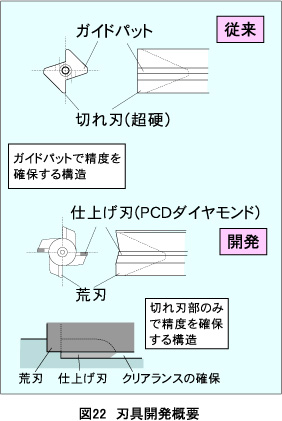
|
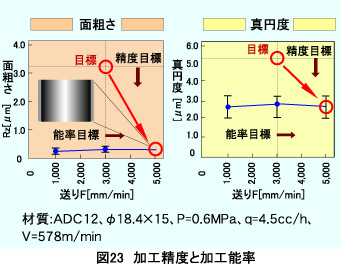
|
3.5 設備技術 |
これまで切削技術に関する開発について述べたが,ドライ加工では設備技術,中でも切屑処理技術が重要である。切削油によって切屑が洗い流されることがないため,治具,ベッドなどへの切屑の堆積,基準面への切屑付着による着座異常などの問題が発生する。これらを解決するためには、設備仕様段階からドライ加工を視野に入れ,ベッド,スライド,治具,カバーなどを設計することが必要である。具体的には,切屑を真下で回収するセンタトラフ構造、ワーク脱着時に基準面上の切屑を吹き飛ばすパッシングエア,治具,切屑カバーヘの潤滑コーティング処理などを行なっている(図24)。しかし,自動搬送ラインでは切屑を落とすために機内洗浄を行なっているものもあり,課題が残されている。
これまで切削加工は,切削油という海水で満たされており,水面のように穏やかであったが,ドライ加工という新しいニーズによって海底のいびつさがより鮮明に認識されつつある。ドライ加工技術開発は,ミストの生成・供給技術,刃具技術、設備技術といったトータルな技術開発と,切削点で起こっている現象を深く掘り下げる基礎研究が重要であり,湿式を含めた切削加工そのものの進歩につながるものと考えている。
今後は,ワンパス加工,ワンツール加工といったさらなる高能率加工技術開発を進めるとともに,切屑処理技術にも力を入れていきたい。
今回紹介した技術が今後のドライ加工技術の発展に役立てば幸いである。
|
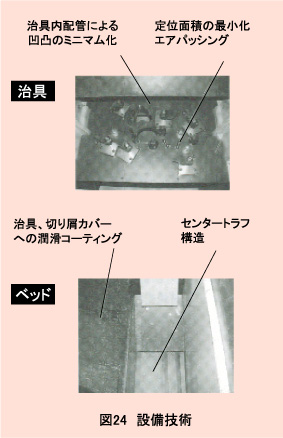 |
参 考 文 献
1)伊藤考治:高精度・省エネ・環境対応形工作機械開発,機械と工具,44,7,21(2000)
2)沢田盛寛:製造現場の環境負荷とその低減,月間・生産財マーケティング,6,A-41(2002)
3)齋藤敏夫:金属加工油の非塩素化に関する調査と市場油の性能について,第26回切削油研究会,(2002)
4)TACO(株)技術資料の一部をモデル化して掲載(2002)
5)オーエスジー(株),超微結晶ダイアモンドコーティングエンドミルカタログ(2002)
6)山本通浩:アルミ材ドライ切削加工技術開発,自動車技術会春季学術講演会前刷集,61,9(2003)
|
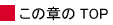 |
本原稿は著者及び初出誌出版社の許可を得て掲載しています。
Copyright esPLANET2004 |