はじめに |
当社は長野県上田市にあるアート金属工業潟Oループの一員として、内燃機関用ピストンを製造している会社である。当社ではピストン製造工程のうち鋳造工程と荒引き工程までを担当し、月産50万個のピストン鋳物を製造している。
環境改善やドライ化というと、大手企業の工場が中心であり、中小企業はコストダウンに奔走し、環境問題の改善からは取り残されているかのような感じを受ける。しかし、当社のような従業員100人の会社でも、ドライ化を推進し、それに伴う大きな効果を上げているので、その改善事を紹介したい。
アルミ鋳造は、高圧で鋳型に打ち込むダイキャスト製法が一般的だが、ピストンは内燃機関の中でも特に強度を必要とする部品であるため、溶湯に圧力をかけずに鋳型に流し込むグラビティー(重力)鋳造が行われている。グラビティー鋳造は圧力をかけずに溶湯を固めるため、金属結晶が均一化し、強度のある鋳物を製造することができる。また、グラビティー鋳造の特徴として、溶湯が固形化する際に、アルミが収縮を起こすため、収縮する鋳物に溶湯を補充するための押し湯を作る必要が生じる。そのため鋳造後、この押し湯を切り落とす必要がある。本稿で紹介するセミドライ加工は、主にこの湯口(押し湯)切断に使用されている。(写真1.2参照) |
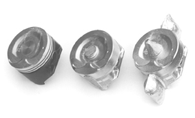 |
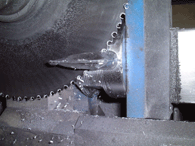 |
【写真1】右から鋳造後 切断後
加工後 |
【写真2】切断部 |
|
従来の方法 |
従来、湯口は製品ごとに専用機で大量の水溶性切削油を使用して切断していたが、この方法には生産性、工場環境ともに問題点があった。生産性における問題点は、@大量ロット生産型の設備であり製品の切替時や刃具の交換に時間がかかり、ライン停止時間が長い。A水溶性切削油の潤滑剤が切り粉などにとられるため濃度が一定せず、刃物の寿命にばらつきが生じた。B水溶性切削油により濡れた湯口を再溶解すると水蒸気爆発を起こすので、乾燥してから再溶解する必要があった。 工場環境面であげると、C水溶性切削油の飛散や漏れによる機械周囲の汚れがひどく、床が滑りやすかった。また、キリコが濡れているために付着しやすく、掃除がしにくかった。 D鋳造炉があるため、年間を通して工場内の気温が高く、水溶性切削油が腐敗しやすく、腐敗臭がした。E切断時の高音域の騒音がひどいなどがあげられた。 |
改善事例 |
環境改善、なかでもドライ化は加工方法そのものの見直しが必要といわれる。当社も、水溶性切削油の弊害をなくすために、機械設備、加工方法の見直しをはじめた。1992年、工場社屋の建替えを契機に切断工程の見直し作業に入った。また、この時期、それまでの大量ロットから小ロット多品種に移行していた。当社で鋳造するピストンの種類は800種類におよび、多品種対応が急務であった。小ロット多品種に対応する設備機械の導入と環境対応を両立するために、様々なトライアルが試みられた。最初に試行したのが、刃物による切断ではなく、プラズマによる溶断だった。成形機から出てきた鋳造品の温度は450℃あり、これを常温まで落として湯口を切断し、再び熱処理炉に入れる。このエネルギーロスをなくすために、高温のままプラズマ切断できないかを検討した。しかし、切断トーチを湯口の形状に倣って移動させなければならず、機械構造が複雑になること。また、アルミは溶融温度が低く熱伝導率が高いため、大きなエネルギーをかけるとピストン本体をも溶融してしまう。といった理由により、困難であることが判明した。やはり刃物による切断が最適であると判断した。
現在、他の業界においても、アルミ切断は超硬チップソーによる高速切
断が主流である。当社が従来行っていた超硬チップソー(コールドソー)による高速度アルミ切断は、切削速度960m/min. 一刃あたり0.01mm、送り720mm/min. の切削条件で行われていた。高速度切断の長所としては良好な切断面と精度が確保できる点である。欠点としては、高速で回転する丸ノコが、高音を発生し、作業者や近隣に騒音をもたらすこと。切削速度が速いため、水溶性切削油が飛び散ったり、浮遊ミストになりやすいこと。切り粉が薄いため、切り粉を再溶解するときに断熱性が高く、歩留まりが悪いことなどが上げられる。しかし、ピストン湯口の切断は後工程にピストンの外周加工が入るため、面粗さや精度はさほど気にする必要がないので、あえて高速度加工をする必要がなかった。そこでこれまでと根本的に考え方を変え、低速度高送りによる切断を試みた。切削速度94m/min.、一刃あたりの送り0.1mm、送り900mm/min. の切断である。丸ノコは一般材(AC8A材)はHSS材のメタルソーとし、丸ノコの厚みを従来は3.0mmだったものを2.0mmに薄くして電力と切り粉に変換する量を少なくした。
機械設備にも工夫を凝らした。まず、多品種小ロットに対応するために、ピストンの大きさによって調整する2枚の丸ノコ間隔を簡単に調整できる機構とし、同時にどのようなピストン形状にも対応できるクランプとした。高送りに対応し、機械全体の剛性を高めたほか、強固なクランプが必要なため、油圧送りと油圧クランプを採用した。(写真3) また、HSS丸ノコは比較的破損(割れ)しやすいため、感度の高い電流検出器を用い工具破損や不良品の発生を防止した。同時にブルーベセミドライシステムを採用することにより、水溶性切削油をなくそうと試みた。このシステムは、鉱油の代わりにごく微量の植物油を用いて切断をする方法で、人体に安全で生分解性のある植物油を用いる。油剤の消費量は、一日8時間連続使用しても丸ノコ1枚あたり30CCという微量で、ドライカットに近い切断が可能になる。専用給油機で、エアーといっしょにミストにして刃物に吹き付ける。(写真4) |
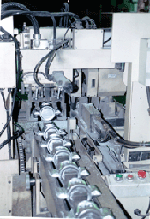 |
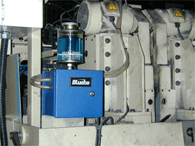 |
【写真3】改善された切断機 |
【写真4】 |
|
改善の効果 |
セミドライ加工システム改善の効果試行錯誤の末に大きな効果が得られ、水溶性切削油の欠点や高速加工の欠点が克服された。効果は生産性を向上できたもの、環境面で改善効果をあげたものがあり【表1】にまとめた。これらの効果は、設備改善とセミドライシステム導入のそれぞれの効果が出たものもあれば、双方の相乗効果によるものもある。主な効果を上げると、
@機械設備の改善とセミドライ加工の相乗効果により、丸ノコの寿命が飛躍的に向上した。【グラフ1】 非常に長寿命になったため、丸ノコを何ヶ月も交換しないこともあり、従来は切断個数で新品に交換していたが、現在は切断機の負荷検出で自動停止するようになっている。
Aセミドライ化によって乾いた切り粉や湯口が出るために、乾燥工程なし
で再溶解が可能になった。(写真5)
B水溶性切削油の濃度管理が不要になり、オイルポットの油量を確認す
るだけになった。
C水溶性切削油の腐敗臭や工場の機械まわりの汚れがなくなり、切り粉
が乾いているので、機械や床が簡単に掃除できるようになった。(写真6)
D月に4500リットル使用していた水溶性切削油がわずか20〜30gの植
物性切削油に置きかわった。
E高速切断の欠点である高音域の騒音が抑えられた。
F短時間での段取替えが可能になったため、従来製品ごとの鋳造ライ
ンに分散していた15台の湯口切断機から、新しい切断装置10台に集
約できた。
Gそして作業者8人で30万個体制から5人で50万個体制へと生産性が
大きく向上したことが最大の効果であった。
セミドライ加工システム改善の効果試行錯誤の末に大きな効果が得られ、水溶性切削油の欠点や高速加工の欠点が克服された。効果は生産性を向上できたもの、環境面で改善効果をあげたものがあり【表1】にまとめた。これらの効果は、設備改善とセミドライシステム導入のそれぞれの効果が出たものもあれば、双方の相乗効果によるものもある。主な効果を上げると、
@機械設備の改善とセミドライ加工の相乗効果により、丸ノコの寿命が飛躍的に向上した。【グラフ1】 非常に長寿命になったため、丸ノコを何ヶ月も交換しないこともあり、従来は切断個数で新品に交換していたが、現在は切断機の負荷検出で自動停止するようになっている。
Aセミドライ化によって乾いた切り粉や湯口が出るために、乾燥工程なし
で再溶解が可能になった。(写真5)
B水溶性切削油の濃度管理が不要になり、オイルポットの油量を確認す
るだけになった。
C水溶性切削油の腐敗臭や工場の機械まわりの汚れがなくなり、切り粉
が乾いているので、機械や床が簡単に掃除できるようになった。(写真6)
D月に4500リットル使用していた水溶性切削油がわずか20〜30gの植
物性切削油に置きかわった。
E高速切断の欠点である高音域の騒音が抑えられた。
F短時間での段取替えが可能になったため、従来製品ごとの鋳造ライ
ンに分散していた15台の湯口切断機から、新しい切断装置10台に集
約できた。
Gそして作業者8人で30万個体制から5人で50万個体制へと生産性が
大きく向上したことが最大の効果であった。
|
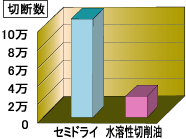 |
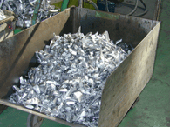 |
【グラフ1】 |
【写真5】切断された湯口 |
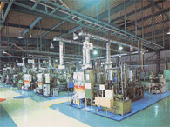 |
【写真6】工場内 |
|
改善結果と効果【表1】 |
生産性側面 |
生産性の向上
【前】従来(水溶性切削油)
【後】改善後(ブルーベ) |
少量多品種対応
【前】段取替えに時間がかかった
【後】段取替えが短時間になった |
生産性
【前】機械15台 8人で月産30万個
【後】機械10台 5人で月産50万個 |
工具寿命
【前】水溶性の濃度によりバラつく。 丸ノコ1枚あたり30,000個カット。
【後】ブルーベ植物油によって飛躍的に向上した。 丸ノコ1枚あたり100,000個カット。 |
再溶解
【前】ローターリーキルンによる乾燥が必要
【後】切り粉が乾いているので、乾燥工程なしで 再溶解できる |
再溶解
【前】切り粉が薄く空気層が多いため、 溶解に時間がかかった
【後】切り粉の比重が重くなり、溶解しやすくなった |
濃度管理
【前】水溶性の濃度管理に手間と時間がかかった。 また、濃度をうまく管理し切れなかった。
【後】オイルポットの油量を確認するだけ |
切断機コスト
【前】300万円/台
【後】600万円/台 |
環境面の改善効果 |
汚れと掃除
【前】切りくずが薄いために、飛散しやすかった。機械回りや床が水溶性切削油で常に汚れていた。また、切り粉が濡れているため、掃除がしにくかった。
【後】切り粉が重いために、飛散しにくくなった。
切り粉が乾いているので、機械や床が簡単に掃除できるようになった。 |
腐敗
【前】腐敗臭がひどかった
【後】腐敗臭がなくなった |
騒音
【前】高音域の騒音が問題化
【後】騒音が抑えられた |
消費油量
【前】原液150L/月(希釈後4500L/月)
【後】20〜30L/月 |
|
考 察 |
改善によって工具寿命が飛躍的に延びたが、そのメカニズムを解明するために観察を行ってきた。推論の域を越えないが、以下のような現象が見られる。
@ 新品の丸ノコを使用しはじめてから、切断ロット1000個位までは、切断が不安定で推移する。これは、刃先の初期磨耗が形成されるまで不安定で推移しているか、あるいは次に書くアルミの溶着が安定していないかであろうと思われる。
A 切断数1000個を超えるあたりから切断が安定する。同時に刃先のエッジにはアルミの溶着が始まる。従来、溶着物質は工具に悪さをするものと考えられていたが、この場合、工具刃先を守る役割を果たしているように思われる。溶着が常に新しいコーティング層として機能しているように観察される。(写真7) 刃先に溶着が発生するため面粗度は粗いものとなるが、後工程で旋削による荒取りと仕上げ加工があるため、当初から面粗さは期待していなかった。むしろ、今まで、刃先への溶着(構成刃先)は、工具に対して悪さをするものという常識を持っていただけに、溶着物質がコーティング層として機能し、刃具寿命を飛躍的に向上させるということは驚きだった。
B ブルーベ植物油は、潤滑性が高いため、チップポケットでカールした切り粉をうまく排出する。最大の効果は、アルミ加工の場合、高潤滑油剤を使用することにより、加工点から切り粉を問題なく排出することであると思われる。ブルーベ植物油を使用しない完全ドライの場合は、チップポケット全体に溶着が広がり、切断そのものができない。
C 一般材(AC8A材)にはHSS材のメタルソーを用いるが、当社の製品の中には近年、難削材といわれているシリコン含有量が20%を超えるアルミ合金(AC9A材等)が増えてきた。これらの製品の切断には超硬チップソー(コールドソー)を用いるが、メタルソーと同じ低速度高送りの条件で切断している。この場合には上記の現象は確認できないが、水溶性切削油を使用していたときに頻発したチップポケットのつまりは、皆無になった。このことからもブルーベの高い潤滑性能による切り粉の排出能力が読み取れる。
改善によって工具寿命が飛躍的に延びたが、そのメカニズムを解明するために観察を行ってきた。推論の域を越えないが、以下のような現象が見られる。
@ 新品の丸ノコを使用しはじめてから、切断ロット1000個位までは、切断が不安定で推移する。これは、刃先の初期磨耗が形成されるまで不安定で推移しているか、あるいは次に書くアルミの溶着が安定していないかであろうと思われる。
A 切断数1000個を超えるあたりから切断が安定する。同時に刃先のエッジにはアルミの溶着が始まる。従来、溶着物質は工具に悪さをするものと考えられていたが、この場合、工具刃先を守る役割を果たしているように思われる。溶着が常に新しいコーティング層として機能しているように観察される。(写真7) 刃先に溶着が発生するため面粗度は粗いものとなるが、後工程で旋削による荒取りと仕上げ加工があるため、当初から面粗さは期待していなかった。むしろ、今まで、刃先への溶着(構成刃先)は、工具に対して悪さをするものという常識を持っていただけに、溶着物質がコーティング層として機能し、刃具寿命を飛躍的に向上させるということは驚きだった。
B ブルーベ植物油は、潤滑性が高いため、チップポケットでカールした切り粉をうまく排出する。最大の効果は、アルミ加工の場合、高潤滑油剤を使用することにより、加工点から切り粉を問題なく排出することであると思われる。ブルーベ植物油を使用しない完全ドライの場合は、チップポケット全体に溶着が広がり、切断そのものができない。
C 一般材(AC8A材)にはHSS材のメタルソーを用いるが、当社の製品の中には近年、難削材といわれているシリコン含有量が20%を超えるアルミ合金(AC9A材等)が増えてきた。これらの製品の切断には超硬チップソー(コールドソー)を用いるが、メタルソーと同じ低速度高送りの条件で切断している。この場合には上記の現象は確認できないが、水溶性切削油を使用していたときに頻発したチップポケットのつまりは、皆無になった。このことからもブルーベの高い潤滑性能による切り粉の排出能力が読み取れる。
|
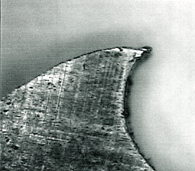
【写真7】刃先の溶着 |
今後の展望 |
湯口の切断工程で大きな効果を上げたため、次工程のピストン外周の
荒引き工程でセミドライ加工を検討中である。荒引き工程は精度・仕上げ面粗度ともに厳しい加工ではないので、湯口切断工程のノウハウが応用できる領域と考えている。しかし、さらに次工程のピストンリング溝加工等の形状加工、ピン穴加工は精度と面粗度が厳しいため、セミドライ化への移行へは更なる研究が必要と考えている |
なお、本論分で紹介した低周速セミドライ切断機をヤシマ金属株式会社の関連会社である(有)蓼北技研工業が、製作しています。詳細は「メーカー紹介」コーナーを参照ください。 |
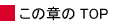 |
Copyright esPLANET2004 |