切削油の歴史とMQLセミドライ加工 |
金属加工が始まった当初から、加工点に少量の油や水をかけて削ると、加工がスムーズに行われることが知られていました。HSS工具とNC化以前の多くの機械では、スプラッシュガード(囲い)もなく、加工点だけに少量の油を流したり、筆で刃先に油を塗ったりしていました。また、当時は、しょうゆ油(もろみから醤油を絞りだした時に出る大豆などに含まれる油)やナタネ油といった植物油を使用していたと、往年の職人さんから聞くことがあります。
1960-80年代にかけて、超硬工具、ついでNC機が普及すると、加工が高速化し、単位時間当たりの切りくず排出量が飛躍的に向上しました。耐熱性の高い超硬工具の出現によって、切削液の目的は加工点の潤滑よりも大量の熱を冷却する目的に変わってきました。それと同時に、大量の切りくずを安定的に押し流すことが重要となりました。そのため、切削油タンクと循環モーターは大型化し、現在では、加工点が見えないほどの切削液を高圧で大量にかけるようになりました。一方、切削液そのものも、油性加工油に代わり、水溶性加工油が主流をしめるようになりました。NC化に伴い、自動運転中に火災の恐れがないことが条件となったからです。
しかし、現在、すべての加工にこうした大量の切削液が必要かどうかの検証はあまり行われていません。省エネ、廃棄物レス、環境負荷低減により、持続的発展が求められる現在、大は小を兼ねるの発想から脱し、切削液に対しても最少適量が求められています。
こうした、加工油の大量使用を改善するために、ミスト加工が提案されています。ミスト加工はノコ盤等では戦前から行われていた加工方法で、古くて新しい加工方法といえます。
環境負荷を低減するために行われているミスト加工には、大きく二つの考え方があるように思います。ひとつは、MQL (Minimum Quantity Lubrication
注1)です。これは、和訳すると「最少量潤滑」であり、現状の油量を低減していき、加工可能な最低限の油量で加工する方法と解釈できます。
もうひとつは、NDM (Near Dry Machining セミドライと同義語)です。これは、ドライ加工をベースに補助的に極微量の加工油を塗布し、ドライ加工のメリットを引き出すという考え方です。加工できるギリギリの油(水)を使用するという点では、両者とも同じ結果になるかもしれませんが、現在、セミドライやMQLという言葉で行われている加工には1時間の消費油(水)量が4mlから2000mlまでの差があり、言葉の定義があいまいになっています。
現在の大量の加工油代替としてミスト加工を考えるとき、最少適量のMQLの発想は汎用性が広く、より多くの現場で適応が可能です。ミスト加工を導入する場合には、そのメリットや加工内容に合わせMQL、NDM両方からのアプローチが必要と思われます。
|
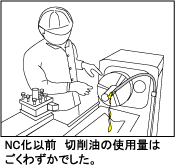 |
切削油の問題点 マクロの視点 -エネルギーと廃棄物- |
地球温暖化防止京都会議において取りまとめられた京都議定書に基づき、先進各国の温暖化効果ガスの削減目標が割り当てられました。2004年10月のロシアの批准により、2005年中に京都議定書の発行が発効する見通しです。日本においては、エネルギー消費量の約50%を産業分野がしめているため、産業分野におけるエネルギー使用の合理化や環境負荷の低減が求められています。特に、工作機械は全国で約70万台が稼動しており、その消費エネルギーの低減が課題といえます。(注2) 下のグラフにあるように、自動車メーカーのデータでは工作機械の消費エネルギーの53%が切削油(クーラント)に関するものであると報告されており(注3)、とりわけ金属加工工場の切削油を低減することが重要な課題となっています。
また、切削油は最終的に金属紛を含んだ汚泥となって産業廃棄物として処理されるため、廃棄物レスの分野からも、その使用量の低減が求められています。切削油の消費量は年間13万トンといわれ、廃油にいたっては年間42万トン(希釈後含む)発生するといわれています。(注4) 環境マネージメント標準のグローバリゼーションとあいまって、切削油の問題は年々クローズアップされています。
|
|
切削油の問題点 ミクロの視点 -汚れと機械設備への負担- |
近年、化学物質に対する管理が厳しくなっています。PRTR法をはじめ、ダイオキシン規制法、土壌汚染防止法。最近では、EUが発動したRoHS有毒物質の使用制限があります。また、切削油についていうと、添加剤として塩素を含有する切削液がダイオキシン発生の原因になると指摘され、1999年以降切削油の塩素フリー化が進んでいます。同時にJIS規格から塩素添加油がはずされる規格変更も行われました。現在、切削油そのものは、一部の添加剤に有害性があるのみで、油剤メーカーも、環境負荷の少ない切削液の開発を行っています。しかし、化学物質に対しては、将来の法規制を視野に入れた先取りの対策と一滴ももらさない密閉型の管理が必要です。現実的には、多くの工場で切削液が部品カゴから滴ったり、工場の床がぬるぬるしています。可能であれば有害物質を使用しないことが、リスク管理面からも重要となります。
リスク管理面から考えると、万一漏洩したり、土壌や河川、海洋に流出した場合でも、環境負荷の少ない生分解性油を使用することが望まれます。生分解性油の代表は植物油または植物油由来の生分解エステルです。しかし、これらの油剤は単位量あたりの価格が高いため、従来のようなフラッドタイプの切削油としてはコスト面で採用しにくく、性能向上のため、鉱油に混ぜて使用されてきました。後述するように、MQLセミドライ加工ならば、使用量が極微量なため、こうした油剤の使用も可能となります。
|
フラッドタイプ切削油の効果
|
大量の切削油は、環境問題や廃棄物問題を除けば多くのメリットを持っており、それをごく微量にまで低減することは簡単なことではありません。
切削油の効果には、@潤滑、A冷却、B穴加工時の切りくず排除、C被削材周辺やテーブル面からの切り屑の除去運搬(フラッシング)といった効果があります。さらに、精密加工分野では被削材の冷却と熱変異防止、機械全体の熱変異防止といった役割も担っています。
多くの方が経験しているように、切削油をかけなければ、工具寿命が悪くなるだけでなく、アルミなどでは工具が折損したり、精度や面粗度が悪くなります。完全なドライ加工がいかにむずかしいかは、切削油を停止してみればすぐにわかります。しかし、切削加工の中には切削油をさほど必要としない加工もあります。
下記は切削油技術研究会が調査した被削材別の使用油種の抜粋です。(注5)
旋盤の場合
鋼 ドライ24%、不水18%、水溶性58%
鋳物 ドライ42%、不水4%、水溶性54%
アルミ合金 ドライ10%、不水20%、水溶性70%
マシニングセンタの場合
鋼 ドライ5%、不水36%、水溶性59%
鋳物 ドライ23%、不水14%、水溶性63%
アルミ合金 ドライ3%、不水17%、水溶性80%
これを見ると、鋳物はドライで削りやすく、アルミには切削油の効果が大きいようです。このように被削材によっても切削油の効果が違ってきます。また、加工内容別では、経験的に断続切削となるフライス、エンドミル系の工具はドライ化しやすく、穴加工であるドリル、タップ、リーマは切削油の効果が大きいといえるでしょう。旋盤加工はその中間といえますが、工具刃先が常にワークの中にあるという点で、連続加工時間が長い場合には冷却の必要性が大きいといえます。
このように切削油の効果は大きなものがありますが、切削油を最小限に抑えたり、MQLセミドライ加工に置き換えることは可能です。しかし、切削油の効果のうち、4番目の切りくずの除去運搬効果(フラッシング)はどうでしょうか。
|
切削油の切りくず除去効果
|
従来は切削油の潤滑効果や冷却効果が重要視されましたが、工具母材の改良やコーティング技術の進歩により、工具の耐熱性が高まった結果、切削油の必要性は相対的に低くなっています。その結果、切削油の主な効果は、潤滑や冷却よりもむしろ、切りくずの搬出となりました。
切りくずの搬出に対しては、工作機械の設計段階からの配慮が必要であり、フラッドタイプの切削油使用を前提にした機械設備を、あとでドライ化することは簡単なことではありません。
MQL専用機を製作しているホーコス株式会社は、切りくず排出性に優れた横型マシニングセンタやバキューム方式による切りくず排出機構を備えたマシニングセンタを開発しており、セミドライ化に対応した設計を行っています。また、NC旋盤では、旧日立精機のCS20旋盤が上げられます。CS20は、チャックが天井についている、いわゆる逆立ち旋盤であり、切り屑の排出が容易であるばかりでなく、機械が熱の影響を受けにくいようにステンレス二重構造の急傾斜機内カバーを設け、切り屑をコンベアに落としていました。また熱を持った切り屑をいち早く機外に搬出するために4倍速チップコンベアを採用していました。セミドライ化やドライ化のためにはこうした設計思想が欠かせません。
2002年にエンジン加工ラインのMQL化を達成したマツダでは、加工そのものはMQLで行っていますが、切りくずの排出は独自のフラッシング方式採用しています。これは防錆効果を持った洗浄液を加工終了から加工物搬送の間に間欠吐出させ、切り屑を洗い流すもので、「省エネルギー切り屑回収技術」と呼んでいます。(注6)
また、潟fンソーでは、既存機の切りくず排出を安価に行う方法として、ステンレス板で新たに傾斜角度の大きいスラント部を作り、エネルギー消費を抑えた自重落下方式を行っています。この場合、実際に切りくずが落下するための角度の評価試験を行い、35度以上(安全を見込み45度)という結論を得ています。(注7)
こうしてみると、切削油の低減またはMQL化のためには、切りくずの排出をどのように行うかを慎重に検討しなければならないことがわかります。
|
切削油の低減・代替方法
|
こうしたプラス面とマイナス面を持った切削油を減らしていくためにはどのような方法があるのでしょう。まず、行われるべきは、切削油の適量・適圧化でしょう。一般にフラッドタイプの切削油ポンプは、大は小を兼ねるの発想で備えられており、加工内容に合った量と圧力にすることが重要です。しかし、この場合、省エネ効果はありますが、切削油レスの他の効果はほとんど得られません。
次に実用化の可能性が高いのは、切削油の搬送にエアーを使用し、ミストにして加工点に吹き付ける方法です。ミスト加工は古くから行われている方法で、特にスプラッシュガードのない大型機を使用し、ワンマシンワンオペレータの重工業では、その作業性のよさから現在でもしばしば見かけられます。しかし、ミストは使用量が多いと飛散が激しく、かえって作業環境を汚すことになります。そうした流れの中で、現在行われているミスト加工には、大きく分けて3種類があります。ひとつは油ミストです。油ミスト(オイルミスト)は潤滑性の高い植物油やエステル油を極少量使用し、ドライに近い加工を行うものが主流です。油剤の使用量は1時間当たり、4ccから100cc(注8)、アルミ高速加工で100-200ccです(注9)。 次に、オイルに冷却用の水を混合してミスト化したものが水+油ミストです。オイルミストのみでは補えない冷却効果を期待して水を加えたものです。この場合の使用量は1時間当たり、油10ccに水1000-1200ccを使用します。(注10) これと似たものに水溶性切削油のミストを噴霧する方法があります。
また、油剤をまったく使用しない完全ドライ加工の研究も行われています。1990年代の後半に一世風靡した冷風加工は、-30度の冷却エアーを加工点に吹き付けて加工するものですが、エネルギー効率の問題と加工範囲が限定されるという問題がありました。また、冷風加工を提唱し中心的存在であった横川和彦、横川宗彦両先生が相次いで逝去されたことで、現在は一部の研究にとどまっています。窒素加工については、工作機械メーカーのエンシュウ鰍ェ1990年代後半に提唱しましたが、明確な効果が期待できないことと、脱酸した窒素を常時使用するため、酸欠の危険性が指摘され、現在は火災の危険性の大きいマグネシウム加工での可能性が残っています。その他に大学レベルで粉末ドライアイス加工が研究されています。
|
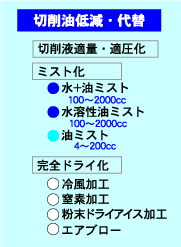 |
ミスト加工の問題点 |
ミスト加工の問題点としては、加工そのものの問題として少量の切削油で加工ができるか、効果を上げられるかという問題があります。それに、加え、切りくず処理のように工程全体を考えたときの問題もあります。これらの問題は、加工内容ごとに、切りくず処理は機械構造と切りくず排出量や形状ごとに考えるべき問題です。ここでは、ミストそのものの問題点を考えてみましょう。
一般にミストというと、マイナスイメージで考えられてきました。「浮遊ミスト」「ミスト対策」「ミスト防止」は、これまで加工工場が取り組んできた衛生上のテーマでした。工場内の空気を清浄に保つことは重要なことであり、作業者の生産性にも影響します。ミスト濃度については、日本産業衛生学会が許容濃度勧告値で鉱油ミストが3mg/m3(1977年)、また、米国のACGIH(American
Conference of Governmental Industrial Hygienists)ではオイルミストの時間荷重平均値を5mg/m3、短時間曝露限界を10mg/m3と定めています。
MQLセミドライ加工によるミストは勧告値に達するようなものではありませんが、工場の建屋や機械密度、換気状態によっては作業者が不快感を感じるものになる可能性があります。昨今のVOC(揮発性有機化合物)抑制の動きとあいまって、浮遊ミストは極力少ないほうが好ましいといえます。また、ミストそのものではなく、油が焼けた切りくずなどに付着したときに発生する油煙についても考慮する必要があります。
対策としては、ファンによる換気、ミストコレクターの設置に加え、作業者の健康に負担を与えないような安全な油剤の使用があげられます。フラッドタイプの研究例ですが、植物由来エステルは、鉱油と比較した場合、蒸気や浮遊ミストになりにくいという報告もあり(注11)、蒸発しにくく、浮遊しにくい油種の選定も必要です。
|
それでは、この後、具体的なMQLセミドライ加工の方法について、述べていくことにします。 |
注1) MQLの語源はMinimum Quantity Cooling 稲崎一郎氏 機械と工具 1996.11 、Minimum
Quantity Lubrication 工学院大学 故横川宗彦氏 1999.9 機械と工具、Minimal
Quantity of Lubricant 静岡大学 鈴木康夫氏 2001.1ツールエンジニア と表現に若干の違いはあるが、最少量潤滑、極微量潤滑と解釈できます。
(注2) NEDO 「エネルギー使用合理化工作機械等技術開発」基本計画 1999より
(注3) トヨタ自動車梶@井川、岩坪、宮崎 機械技術 1999.5
(注4 )NEDO 「エネルギー使用合理化工作機械等技術開発」基本計画 1999より
(注5)機械と工具1998.1桜井浩樹 第55回切削油技術研究会総会資料(1993)
(注6)平成14年省エネルギー優秀事例全国大会、ECCJ ホームページより
(注7)月刊トライボロジー 2004.2 .潟fンソー 永田雅亨、森田浩充
(注8)フジBC技研 ブルーベカタログ、
(注9)2004自動車部品生産システム展先端技術フォーラム ホーコス梶@槇山正
(注10)2004自動車部品生産システム展先端技術フォーラム 大同メタル工業梶@丹羽小三郎
(注11)Mercwdes-benz AG, Fuchs Mineraloelwerke GMBH ,Low emission lubricants
final report
|
 |
Copyright esPLANET2004 |