外部ノズル給油 |
ミストによる加工は、工具の外からノズルでミストをかけるという方法が昔から行われてきました。このミスト給油方法を「外部ノズル給油」と呼び、後述する内部給油と区別します。ノズルによるミスト給油の原理は霧吹きと同じで、内燃機関のキャブレター、塗装、薬剤散布などで利用されてきました。切削油の塗布用にも簡単なものから高価なものまで、いろいろなものが市販されています。大きく分けて@ベンチュリーの原理で負圧を利用して液体を吸い上げ噴霧する方法、Aタンクにエアーで加圧し、吐出された油剤とエアーを混ぜ合わせて噴霧する方法、Bポンプ(可変ポンプまたは定量シリンダ)を使用し、一定量の油剤をノズルに送り込み、ノズル内でミストにするもの。価格的にも4万円くらいから20万円くらいまでのバリエーションがあります。また、ミストとして使用できる油剤も、油性のみのもの、水溶性も使えるものがあります。それぞれのミスト装置が異なったコンセプトで開発されており、吐出量にも差があります。これらのミスト給油機の選択には迷うものがありますが、どのような基準で採用したらよいでしょうか。ひとつは、ミスト装置が吐出できる油量のうち、最少量と最大量の「最少量」の方に気をつけていただきたいということです。基本的にはMQLというのはできるだけ少ない油剤で加工しようというものですので、ミスト装置がどれだけ少ない量で安定的に塗布できるかが重要です。ミスト装置は一般的には多くのミストを強く出すと安定しますが、エアーと油を絞り込んでいくと吐出が不安定になります。特に、@のベンチュリー方式では負圧を得るためには一定のエアー流量が必要なので、エアーを絞り込んでいくと不安定になりやすくなります。また、生成されるミストの粒の細かさも問題になります。あまり細かいとエアーと一緒に飛散し、浮遊ミストを増やし、工場の空気を汚しかねません。
上記の外部ノズル給油装置とはコンセプトを異にするミスト装置があります。それは、可変の混合比率で油と水とをノズルへ送り込み、油、水、エアーの混合ミストを塗布する機種です。これは、加工点の潤滑効果と同時に冷却性能を狙ったもので、給油機そのものもポンプを2台搭載した大掛かりなものになっており、価格も50万円くらいから200万円くらいします。一般的なセミドライ加工は油を1時間当たり、4mlから100ml程度の範囲で塗布しているのに対し、この方式は同量程度の油に100から2000mLくらいの水を混合させて塗布します。
|
|
内部給油 |
ノズルで工具の外部から噴霧する場合は、さまざまなバリエーションから選択することが可能ですが、使用できる機械設備は限られてしまいます。工具の外から噴霧できる機械は上の図にあるようにバンドソーや丸ノコ盤、単能機、ブローチ盤のように単一の工具を使用する設備に限られてしまいます。ATC(自動工具交換装置)のついた機械の場合、刃物の長さが変わるとノズルが追随しなくなってしまいます。また、穴加工の場合は、ノズルで工具の外からかけても効果は少なく、オイルホール付工具を使用して、刃先にミストを送り込む必要があります。こうした要請から1990年代に「内部給油方式」と呼ばれるミスト塗布方法が開発されました。これは、従来のクーラントと同じように、機械の中からミストを吐出させる方法です。マシニングセンタではスピンドルスルーで、NC旋盤ではタレットを通してミストを吐出させる方法です。
しかし、ミストの特性として、長い配管内にミストを通すと配管内壁にミストが付着し、液状化を起こし、レスポンスが悪くなるという現象が見られます。特に、高回転で回っているスピンドルのドローバーの中を通すと遠心力のためにミストが管壁に張り付いて出てこないという欠点が生じます。
|
内部ミキシング |
こうしたミストの特性をミスト搬送の限界ととらえ、スピンドル後端の工具直近で油とエアーを混合して吐出する方法があります。工作機械メーカーのホーコス株式会社が開発し、特許を取得している方法です。スピンドル内をエアーと液体の2系統にし、ロータリージョイントも2系統にしています。この方法の長所は機械内配管の影響を受けず、スピンドル内の遠心力の影響を受けにくく、ミスト量を無限に増やすことができるという点です。コストを別にすれば、技術的には最良の方法といえるでしょう。
|
 |
外部ミキシング |
一方、液状化現象が起こしにくいミスト給油機も開発されています。装置によってミスト粒径を1-4ミクロンにまで細かくすると、配管内壁にミストが付着しにくくなります。ドライフォグと呼ばれる微粒子ミストです。従来のクーラントラインを利用してミストを刃先まで送り込めるので、既設の設備にも取り付けができるという長所があります。また、スピンドルを持たないNC旋盤のような機械設備の場合には効果的といえるでしょう。欠点としては、配管形状によっては多少の液状化が見られ、またスピンドルスルーの場合には回転に応じてミスト量が減る傾向があります。また、エアーによって微粒子油滴を搬送するため、通過エアー量により吐出できるミスト量に限界が生じます。
|
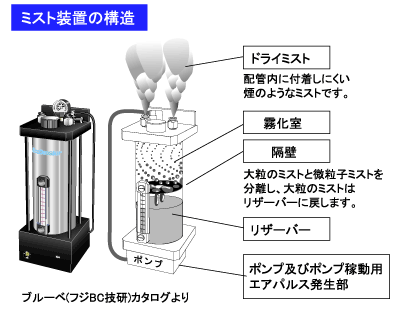 |
液状化について |
ここで、液状化について簡単にコメントしておきます。液状化は配管内で乱流が起きることによって発生します。ナイロンチューブのような内径に差がなく、極端な曲がりのない配管では乱流は発生せず、液状化もほとんど起きません。一方、金属配管のエルボ、チーズ、配管径の異なる継ぎ手があると乱流が発生し液状化しやすくなります。また、スピンドル内を通す場合、スピンドル径にもよりますが、およそ3000-6000回転くらいからミストに影響が出始め、遠心力の影響を受けて、ミスト吐出量が減少する傾向があります。特に問題となるのは、配管内にチェック弁(逆止弁)がある場合で、チェック弁は完全なオリフィスとなるため、非常に液状化しやすくなります。
|
|
出口断面積の検討 |
ドライフォグを生成するミスト装置を使用する場合の注意事項について申し上げておきます。配管内の液状化を防止するため、極微粒子のミストを作るミスト装置が販売されていますが、このミスト装置から出るミストは配管内に付着しにくいドライフォグです。このミストは配管内を通過して工具先端から出るときに、ドライフォグのまま出てしまうと工具にも被削材にも付着せずに飛散してしまいます。そこで、ミスト吐出口で絞り(オリフィス)状態を作り出して、意図的に液状化状態を作り出し、ウェットミストに変えなければなりません。ミスト装置メーカーでは、最終的にミストを吐出する出口の出口断面積を制限しています。ミストの出口断面積はおよそ0.5mm2から5.0mm2の間であり、それ以上の断面積になると白煙のようなドライフォグが出てしまいます。また、最終部で、ドライフォグをウェットミストに変換するには流速が早いほうが有利なため、エアー圧力が高ければ、断面積の許容値は広がります。
一般的には、ドリルの場合、オイルホール径が1.8mmを超えると、2穴の断面積が5mm2を超えるため、工具メーカーにもよりますが、径12-16mm以上のドリルを使用する場合は注意が必要です。また、エンドミルなどでは、油穴の開いているものが少ないため、ノズル付コレットから出す場合がありますが、この場合にも出口断面積の検討が必要です。
一方、出口断面積が小さい小径ドリルなどの場合はどうでしょうか。小径ドリルの場合、油穴径が非常に小さいため、通過エアー流量が極端に少なくなり、ミストを搬送しにくくなります。この場合は、各装置メーカーとも工夫を凝らし、専用の給油装置を開発したり、バイパスバルブを設けるなどしていますので、各メーカーに相談するといいと思います。
|
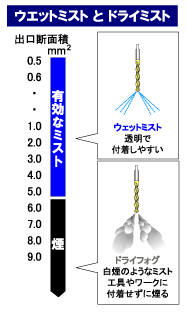 |